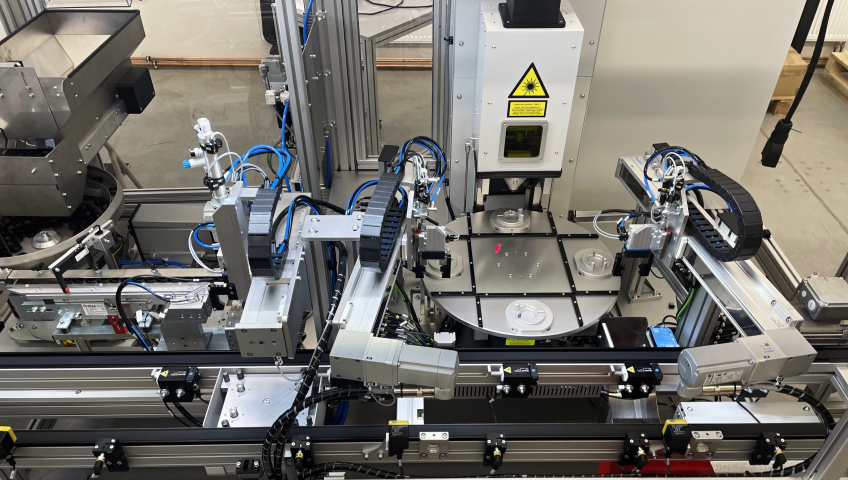
VIDEO: Automatisierte Station für die Bearbeitung von Verstärkerventilen
Im heutigen Wettbewerbsumfeld sind Effektivität, Produktivität und Qualität von höchster Bedeutung. Durch die Beschleunigung und Effektivierung von Fertigungsprozessen kann die Automatisierung das Produktivitätsniveau entscheidend steigern. Aus diesem Grund entschied sich auch unser Kunde dazu, seine Fertigung zu automatisieren. Hierfür haben wir zwei vollautomatisierte Produktionsanlagen zur Bearbeitung von Verstärkerventilen, die in den Kühlsystemen von LKWs zum Einsatz kommen, entwickelt. Diese von LINTECH gefertigten Anlagen kommen an Position drei und sieben in der Fertigungslinie des Kunden zum Einsatz.
Entwurf der automatisierten Anlagen:
Um die individuellen Anforderungen des Kunden zu erfüllen, haben wir zwei vollständig automatisierte Segmente entworfen, die in die bestehende Fertigungslinie integriert werden können.
Die Anlagen sind beidseitig mit einem geschlossenen Transportsystem verbunden, das den kontinuierlichen Materialfluss sicherstellt. Diese Art und Weise der Konstruktion ermöglicht effektive Bearbeitungsvorgänge bei minimalen Wartezeiten und maximalem Durchsatz.
Anlage Nr. 1: Montage und Verschweißen von Plastikringen
Die erste von uns produzierte Anlage befindet sich an dritter Stelle in der Linie des Kunden und führt das Verschweißen von Kunststoffringen an den Ventilkörper durch. An dieser Stelle der Produktion werden in Summe vier verschiedene Teiletypen geschweißt, von denen jedes eine andere Orientierung des angeschweißten Ringes erfordert. Um dieser Herausforderung gerecht zu werden, wurde ein komplexes System geschaffen. Dieses nutzt einen Vibrationsbehälter, der mittels Umlaufrillen und einem nachfolgenden Mechanismus für eine exakte Positionierung sorgt, wobei der Ring mittels Fangarmen an der Rotationsaxe um den nötigen Winkel gegenüber der Ausgangslage im Vibrationsbehälter gedreht wird. Ein störungsfreier Arbeitsablauf wird durch das automatische Nachfüllen der Ringe in den Vibrationsbehälter aus einem ausreichend großen Bunker heraus gewährleistet.
Sobald der Ring ordnungsgemäß mit einer Kraft von 250N eingepresst wurde, bewegen sich das Teil und der Ring an die Schweißposition. Unter kontinuierlichem Druck von 700N wird das Teil in eine Drehbewegung von 12 Umdrehungen pro Sekunde versetzt, während unser 300W-Schweißlaser seine Arbeit aufnimmt. Der gesamte Laserprozess, der mittels Pyrometer und Hitzesensor überwacht und anschließend ausgewertet wird, dauert nicht einmal drei Sekunden. Nach dem Abkühlen wird das Teil mit Hilfe einer Vorrichtung wieder auf das Förderband gelegt. Durch die Nutzung eines Karussellsystems laufen die Schritte des Platzierens, Schweißens und Zurücklegens auf das Fördersystem parallel ab, sodass eine Verkürzung der Zykluszeit auf 12 Sekunden mit entsprechend erhöhter Gesamtproduktivität erreicht wurde.
Anlage Nummer 2: Montage und Schweißen von Ventilspulen
Unsere zweite Anlage, die an siebter Stelle in der Fertigungslinie zum Einsatz kommt, führt die Montage von Spulen im Verstärkerventil durch. Nach seiner Ankunft an diesem Fertigungsschritt wird das Teil einer gründlichen Kontrolle unterzogen, um sicherzustellen, dass es vollständig und richtig aufgebaut ist. Die Spulen sind auf dem Förderband willkürlich ausgerichtet. Nachdem sie in die richtige Position gedreht wurde, wird die Spule mit einer Kraft von 200N an das Ventil angepresst. Die komplette Einheit wird mit Hilfe eines Manipulators im Karussell platziert, wo sie unter einem Anpressdruck von 2000N in einer Drehbewegung verschweißt wird. Der Schweißprozess wird sorgfältig gemonitort, wobei der finalen Einpresshöhe nach durchgeführter Schweißung besondere Beachtung zukommt. Diese präzisen Messungen werden mit vorgegebenen Werten verglichen, um die Qualtiätsnormen einzuhalten. Sollten Abweichungen festgestellt werden, wird das betroffene Teil mittels Manipulator automatisch aus der Fertigungslinie ausgeschleußt und in ein NOK-Fach umgeleitet. Somit wird sichergestellt, dass nur fehlerfreie Teile im Fertigungsprozess weiter veredelt werden.
LINTECH ist sehr stolz darauf, die anspruchsvollen Anforderungen seiner Kunden und Partner erfolgreich erfüllen zu können. Dieses erfolgreiche Projekt unterstreicht die Bedeutung maßgeschneiderter technischer Lösungen für die Erzielung von Produktionseffizienz im heutigen wettbewerbsintensiven Markt.