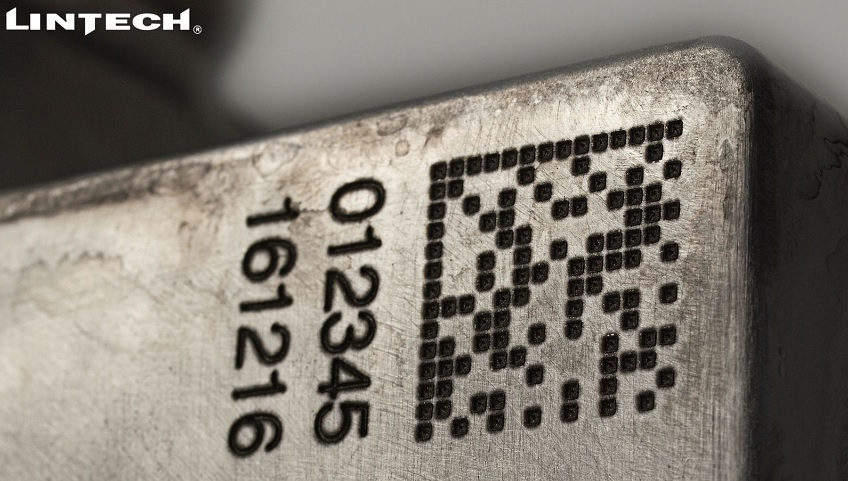
Deep laser engraving
Deep engraving is understood to mean applications where the engraving depth is greater than 0.1mm.In principle, laser engraving resembles the application of a laser description, however, in order not to create a contrast on the material, but to vaporize it and create deep patterns. Since the laser beam can influence the material very precisely due to its small size, very detailed patterns can be made, most often laser engraved with different graphics, alphanumeric text and barcodes, especially 2D codes for product identification. Laser also achieves excellent wall perpendicularity, helping to create shadows in engraved areas. This is an important aspect for creating the right contrast in the pattern, especially when reading 2D barcodes with readers.
In addition to accuracy, the process boasts excellent scalability. The most common procedure is to evaporate a layer of material with optimal parameters and repeat this procedure cyclically until the desired depth of pattern is reached. In this case, the number of iterations is dependent on the depth requirement (process time becomes dependent variable) or the time requirement (the dependent variable becomes the depth). Very often, especially when it comes to mass production processes, emphasis is often placed on depth and at the lowest possible time limit for the entire operation. Finding the right parameters for optimal process equilibrium in such cases is not a simple matter and requires some labor. The engraved area is logically also one of the most important aspects of time consuming that tells you if the application time is measured in seconds or in tens of minutes.
Depth engraving is most often used to identify parts where a very high wear burden is expected, or where identifiability is to be maintained even after subsequent surface treatment (the surface of the material has to be engraved or should be covered with a layer of a certain thickness) .
As mentioned above, laser engraving is done by pulse lasers, which usually engrave different types of metals. As pulse lasers are most commonly used fiber lasers with an average power from 20W higher. Higher performance, of course, provides more efficient material removal and can significantly shorten process time, but it can also negatively affect design. And that´s why the resulting material is more strongly extruded into the surrounding area of the engraved zone, in the form of a melt at the boundary contour and it form then small iron scales. Besides the proper type of laser source, it is also necessary to use a suitable optics, a selection of suitable process components, as well as suitable parameters. Their settings lie on the supplier of laser technology.
Due to the relatively aggressive course of application, it is important to ensure as the protection of people around the laser system, like the protection of key laser components. Covering the entire device according to safety standards is, as with other laser applications, a matter of course. However, increased attention should be paid to intensive extraction of sublimated material. On the one hand, it may contain components capable of damaging human health by inhalation, at the same time it may cling on the laser optics and cause its degradation. During very intensive engraving, the suction itself may not be sufficient, and it is also appropriate to supplement it with the addition of pressurized air - the so-called air knife that deflects the sublimed material from the optics towards the suction tube.